

All You Need to Know About Mechanical Plugs and Connectors – A Complete Guide
Learning about mechanical stuff such as plugs and connectors might not be the most exciting activity you’ll have on today’s schedule, but it’s something you should know more about.

All property owners must have at least elementary knowledge concerning mechanical plugs and connectors, so they can quickly get around to fixing minor things around their home without having to pay large sums of money to professionals. However, experts can learn a lot from this blog post too.
Here, you’ll find a complete guide on everything you need to know about mechanical plugs and connectors, regardless of whether you’re a professional or not. As a result, you’ll rarely find yourself in a situation where you don’t know what to do. Let’s jump straight into it!
About mechanical plugs
First things first, let’s focus on mechanical plugs. If you need to conduct pipeline inspections and repairs, you can hardly do so without having the right tools by your side. Not using or using the wrong mechanical pipe plugs can result in cracked, damaged pipes and ruined tests, which will ultimately cost you a lot of money and time.
To avoid this from happening, all you need to do is invest in the right tools for the job. That’s where mechanical plugs come in handy. They are tools that you can install on pipes. When installed, the plugs are flushed with air or water to reveal or find leaks, corrosion, or any other weaknesses within the system.
If you’re unsure how to use this tool or what it can help you with, this is the ideal place to learn everything you need to know about mechanical plugs.
How mechanical plugs work
When shopping for mechanical plugs, you’ll find numerous mechanical plug shapes and sizes at your disposal. These tools are designed to fit a wide range of different pipelines, so you’ll need to do a proper inspection of your pipelines before finding out which type of mechanical plug you need.

Once you establish the required mechanical plug type, shape, and size, you can browse products from a large selection and choose your preferred option. With a bought mechanical pipe plug, it’s time to establish how these tools work.
Essentially, mechanical plugs seal the pipes, thus creating pressure build-up in a particular part of the system. Testing how the pipes handle pressure is essential for homeowners, especially in a building. Depending on the number of users and the pressure put on the pipelines, it’s not uncommon for pipes to crack or cause more significant damage to the entire system.
With the help of mechanical plugs, you can quickly test this and avoid a more significant amount of damage. Most mechanical pipe plugs come with nuts and bolts that ensure the plug is secured, sealed, and leakproof. That’s the main reason why these plugs are called mechanical – they require you to manually tighten the nuts and bolts first to center the plug and then push the seal into place.
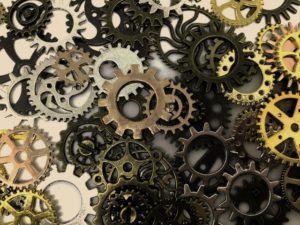
Using mechanical plugs might not be the most straightforward task on your plate, but the benefits certainly outweigh the difficulties that might come with this complex task.
Uses of mechanical plugs
Plumbers and other pipeline workers use mechanical pipe plugs. These tools are created to test a piping system. When inspecting a specific pipe for leakage, corrosion, cracks, or any other kind of damage, the inspected part of the pipe must be sealed. That means experts can freely work on the desired piping area without disturbing or causing damage to the rest of the system.
By controlling the nuts and bolts on the plug, you can create a leakproof and airtight seal. That way, you can flush air and water through the pipe, and the problem areas are immediately detected.
Since this isn’t a simple task, you’ll probably need other tools to control the nuts and bolts located on the plug. Add additional tools to your shopping list if you don’t happen to have a screwdriver or pliers in your toolkit.
Here’s a quick guide on operating mechanical plugs and putting them into the desired location:
- Tighten restraint screws that center the plug and enable full pressure restraint;
- Tighten the mechanical seal nuts that ensure the seal remains leakproof;
- Test the plug by filling it with liquid and letting the air out through designated vent ports;
- Close the vent ports and test the system’s pressure.
Benefits of mechanical plugs
Now that you know more about mechanical plugs, we must mention some of the most significant benefits of using this tool. Firstly, one of the most apparent benefits of mechanical plugs is their flexible use case. Besides being helpful during pipe testing, you can also use these plugs for stack testing or vent testing.

Secondly, although you can choose between inflatable and mechanical plugs, the mechanical ones come with their unique perks. For instance, they don’t deflate over time and can last you a long time, even when used for the most demanding tasks related to high pressure.
Thirdly, mechanical plugs are made from sturdy, durable, and quality material that doesn’t rust or cause any damage to the system where it’s used. That makes them an ideal solution for testing old, sensitive pipelines.

Installing mechanical plugs is a must whenever you need to test and inspect your pipes. This versatile tool will provide you with the most accurate results regarding your piping system without causing any damage. You’ll be able to detect minor issues and resolve them quickly and affordably.
About connectors
Moving on to connectors, they’re a story for themselves. There are countless connector types you can choose from. Every shop carries different connectors – circular, power connectors, header, PCB receptacles, and numerous others. Because of that, the way to pick the right one can be pretty tricky.
However, with the right guide by your side, you’ll be able to differentiate the slight nuances found in these connectors and choose the one you need. If you’re searching for a specific connector but don’t know where to start, this guide will provide you with all the answers.
Electrical requirements for connectors
One of the first things you need to check when choosing connectors is the electrical requirements. From the number of signals to voltage specifics to frequency and currents supported, there are plenty of details only in the electrical requirements for connectors.
For example, connector signals can be analog, digital, power, or the combination of all three. Furthermore, analog and digital signals can support low or high frequency. The list can go on. That’s why it’s essential to single out all the electrical requirements you need your connector to have.
Connector electrical requirements come with numerous specifications, including:
- Signals with high frequency can couple with other nearby wires or use coaxial connection;
- Low-frequency analog signals sometimes need shielding;
- High current paths typically require multiple pins or larger wires;
- High voltage pins usually use high dielectric strength materials or take clearance and creepage distances into account.
Furthermore, it’s important to remember that some signal combinations aren’t possible for certain connector types. For instance, some connectors have only electrical signals, while others come with fiber-optic connections.
In addition to that, some connector applications require liquid or gas lines. If you want a design that requires everything to be connected to a single connector, you’ll most likely need to implement a custom-made solution.
Size and space constraints of connectors
Since the Industrial Revolution, continuous progress has been made in technology and electronic equipment, especially when size and space reduction took off over the last few years.

IAs a result, modern technology and electronic equipment have almost nothing to do with their predecessors. From giant boxes that took the space of entire rooms to minimalistic wearables, computers are only one example of tech size and space constraints.
With that being said, although reducing in size, connectors have significantly grown in power. Today, even the miniature low-frequency connectors are more potent than most connectors used in the past.
Operation of connectors in extreme conditions
Extreme mechanical conditions typically include shock, vibration, temperature, and others. Because connector systems often meet these extreme conditions, they have unique features as part of their design.
Some connectors are even specially designed for extreme conditions, and these tools usually incorporate threaded coupling that offers the maximum level of support to the wiring harness or similar features. These properties serve to provide shock and vibration resistance.
The resistance ratings are often found in the specifications or at the top of the datasheet if a specific product has been specifically created to withstand extreme mechanical conditions.
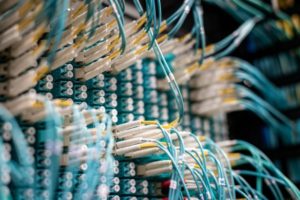
Unique materials are used to insulate and protect the connector and all its contacts in temperature. Regardless of whether you’re using your connector indoors or outdoors, these materials and insulation enable connectors to be mated and unmated time and time again, without decreasing their quality, durability, and reliability. However, users are advised to pay attention to the optimal operating temperature range and stay within the boundaries.
Importance of connector sealing
We already mentioned unique materials and insulation is used for connectors to protect them from extreme mechanical conditions. However, connector sealing has other essential features as well. For example, some requirements must provide additional protection to seal connectors from liquids, chemicals, or dust.
While even the most common connectors today come with a certain level of sealing, which protects the equipment from occasional splashes, some connectors require significantly better seals.
Some connectors may require additional sealing that adds to the protective layer and keeps dust, water, and other elements away from the core of the connector. In exceptional cases, connectors also must endure high pressures and temperatures. It’s common in medical and food industries where sterilization plays a significant role.
Once you learn which level of protection you need for your connector, you can check the IP rating number to learn more about the specific connector and its protection.
Mandatory industry standards related to connectors
There are all kinds of industries operating in the present-day world. While all industries come with their unique specifications and demands, the medical, food, and cosmetic industries are the most demanding as they require the highest levels of cleanliness and sterilization.
If you’re looking to purchase connectors that’ll be used in one of such industries, you need to pay close attention to all medical and FDA standards your connectors must meet. Even if there aren’t any specific details on connectors, the specifics related to the equipment connected to the connector system could sway your decision.
On the other hand, the automotive industry may not require the sterilization of its connectors and appliances. Still, it certainly requires robust connectors that come with high frequency and voltage, mainly for automotive companies working with electric and hybrid vehicles.
Other industries come with their unique requirements too. Don’t forget to check these out to avoid investing in a connector you won’t get much use out of.
Connector levels of reliability
When choosing a connector, reliability is another important feature you have to consider. Frequently mating and unmating the connector can easily damage if the connector isn’t reliable enough. Again, choosing the level of reliability comes down to the connector’s use case. Connectors intended for one-time use won’t need to possess the same level of reliability as connectors used for a long time. Namely, connectors in a vehicle should last as long as the car itself, so the requirements are slightly different.
Because of this, connectors often come with MTBF (Mean Time Before Failure) or MTTF (Mean Time To Failure) details in the specifications that approximately calculate the estimates of the connector’s life. It can come in quite handy when choosing a connector for a specific purpose.
Even though precise calculations are almost impossible to determine, approximates are more than enough to make an intelligent choice.
The bottom line
Both mechanical plugs and connectors come with unique features and specifics. However, as some of the critical electronic elements in today’s technology, it’s essential to learn the basics of these pieces of tech equipment. With this helpful guide, you’ll have all the necessary information in one place.
Furthermore, you’ll be able to decide on the best products for specific applications without wasting plenty of time on additional research.